In the field of stamping automation, the servo roller feeder has always played a crucial role, not only improving production efficiency, but also ensuring product quality. Our company’s RNC series servo roller feeder has such advantages, providing strong support for the stamping production of many enterprises.
I. Diverse Specifications to Meet Diverse Requirements
The RNC series includes models such as RNC – 200, RNC – 300, RNC – 400, RNC – 500, and RNC – 600, and is further subdivided into different versions like HA, HB, and F. Each model has specific parameter settings in aspects such as material width, thickness, maximum feeding length, feeding accuracy, roller pressurization method, release method, and feeding height. For example, the material width has multiple options ranging from 200mm to 600mm. In terms of material thickness, the maximum thickness of the RNC series – HA and RNC series – F is 3.2mm, while that of the RNC series – HB can reach 6.0mm. The maximum feeding length for all models is 9999.99mm, and the feeding accuracy can be controlled within ±0.2mm. The rich variety of specifications and models allows enterprises to precisely select a suitable feeder according to the characteristics of the materials they produce and the requirements of their production processes, thus meeting diverse production needs.The following is the video of the specific work:
Mode | Coil width | Coil Thickness | Coil Thickness X Coil width | Pass Line | Releasing Performance | Motor |
RNC-100 | 20~100 | 0.1~3.2 | 3.0×100/3.2×80 | 70~170 | ~200 | AC 0.4 |
RNC-200 | 20~200 | 0.1~3.2 | 2.3×200/3.2×80 | 70~170 | ~200 | AC 0.4 |
RNC-300 | 20~300 | 0.1~3.2 | 2.0×300/3.2×80 | 70~170 | ~200 | AC 0.75 |
RNC-200HA | 20~200 | 0.3~3.2 | 2.3×20013.2×80 | 70~170 | ~80 | AC 0.4 |
RNC-300HA | 20~300 | 0.3~3.2 | 2.0×300/3.2×80 | 70~170 | ~80 | AC 0.75 |
RNC-400HA | 20~400 | 0.3~3.2 | 1.6×400/3.2×50 | 70~170 | ~80 | AC 0.75 |
RNC-600HA | 20~600 | 0.3~3.2 | 1.2×600/3.2×50 | 70~170 | ~60 | AC 1.3 |
RNC-800HA | 20~800 | 0.3~3.2 | 1.0×800/3.2×50 | 70~170 | ~60 | AC 2.9 |
RNC-200F | 20~200 | 0.2~3.2 | 1.0×800/3.2×50 | 70~170 | ~200 | AC 0.4 |
RNC-300F | 20~300 | 0.2~3.2 | 2.3×200/3.2×100 | 70~170 | ~200 | AC 0.4 |
RNC-400F | 20~400 | 0.2~3.2 | 2.3×300/3.2×80 | 70~170 | ~150 | AC 0.75 |
II. Easy to Operate with Practical and Efficient Functions
The operation panel has a simple design and clear functions. The power indicator light is used to display the power status, the power switch controls the power supply of the whole machine, the manual/automatic selection switch can quickly switch the working mode, and the emergency stop switch is the key to ensure production safety. It can quickly stop when encountering abnormal conditions.
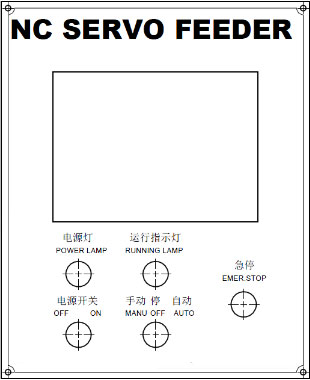
The touch screen has a friendly operation interface. The boot screen displays the basic content such as mechanical model and manufacturer information. Press “Start” to enter the automatic operation screen. In the automatic operation screen, the feeding length and speed are displayed in real time, and the production quantity is automatically counted. Set the production quantity before production. When the set value is reached, the equipment will automatically stop and jump out of the alarm screen. Press “Alarm Reset” to restart. The manual screen is convenient for manual feeding, returning, relaxing, clamping and other operations. Before operation, manual operating parameters need to be set, such as manual feeding speed. The parameter screen is used to set key parameters such as feeding length, automatic speed, manual speed, etc., and can also set the oiling time of the material oiler. In addition, there are also technical parameter screens, multi-segment screens, etc., which can be set for acceleration and deceleration time, relaxation function selection, and multi-segment feeding functions to meet the needs of complex production processes.
III. Safety Assurance to Ensure Worry Free Production
Safety is of utmost importance in production. Ruihui servo roller feeder has comprehensive safety measures. In terms of the working environment, operators are required to wear safety work clothes and safety shoes. Wearing clothes that are easily caught by the machine is prohibited. Keep the working environment and the machine clean and tidy. Equip with fire fighting and first aid facilities. Return tools to their original positions after use. In the preparation stage for operation, check the machine screws, air pressure source and power supply before daily work. Confirm the safety of surrounding personnel before starting the machine and ensure that the machine actions are completed before shutting down. During operation, it is strictly prohibited to touch the movable parts and materials of the machine. Removing the cover is prohibited. Even when the machine stops running, hands cannot be inserted into the opening of the roller. And cleaning supplies cannot be used when the machine is running. When inspecting and adjusting the machine, turn off the power supply and air pressure source and set up warning signs.
IV. Maintenance and Inspection to Maintain Equipment Performance
Regular maintenance and inspection is the key to ensure the stable operation of the feeder. Daily inspection of screws, air pressure pipes, water filters, pressure regulators, gears of transmission mechanisms, extension wiring, feeding rollers, panels, solenoid valves, etc. is required. Such as checking whether the screws are loose, whether the air pressure pipes are leaking, whether the water filters are draining, whether the pressure of the pressure regulating valve is at the recommended value of 3Kg/cm2, and whether the gears need to be lubricated. Timely detection and treatment of problems can effectively reduce equipment failures and prolong the service life of equipment.
Item | Spot check position (name) | Check the content |
1 | Position screw | Whether loose |
2 | Air pressure pipe | Whether a flat |
3 | A 2 point combination filter | drainage |
4 | The pressure regulating value | Suggest 3 kg/c ㎡ |
5 | Drive gear | Lubrication (ISO VG 320~VG370) |
6 | Extension connection | Is it broken? |
7 | Feed roller | Whether dirty or dirty should be cleaned |
8 | panel | Switch, light, display is normal. |
9 | Solenoid valve | Whether dirty or dirty should be cleaned |
V. Troubleshooting to Resume Production Rapidly
In the production process, if a fault occurs, the Ruihui servo roller feeder has a detailed troubleshooting guide. For example, if the equipment fails to start, possible causes include no power connection, power switch not turned on, circuit breaker tripped, or the emergency stop button being pressed. Corresponding solutions are to connect the power cord and turn on the power switch, reset the circuit breaker, and rotate the emergency stop button to the right. Issues such as material slithering, slipping, pressing damage, poor relaxation, and poor feeding accuracy can also be addressed based on specific causes like roller pressure, cleanliness, material quality, and equipment stability, with appropriate measures taken to quickly resume production.
The Ruihui servo roller feeder, with its diverse specifications, simple operation, comprehensive safety features, effective maintenance inspection mechanisms, and convenient troubleshooting methods, plays a crucial role in stamping automation production. It is an essential tool for companies to improve production efficiency and ensure product quality.ui