A manipulator is a mechanical device that can be active or controlled by humans; an industrial robot is a type of automation equipment, a manipulator is a type of industrial robot, and there are other methods for industrial robots.
The stamping Multi-station manipulators is based on automation equipment and is specially developed for stamping automation and unmanned production according to the characteristics of stamping production.
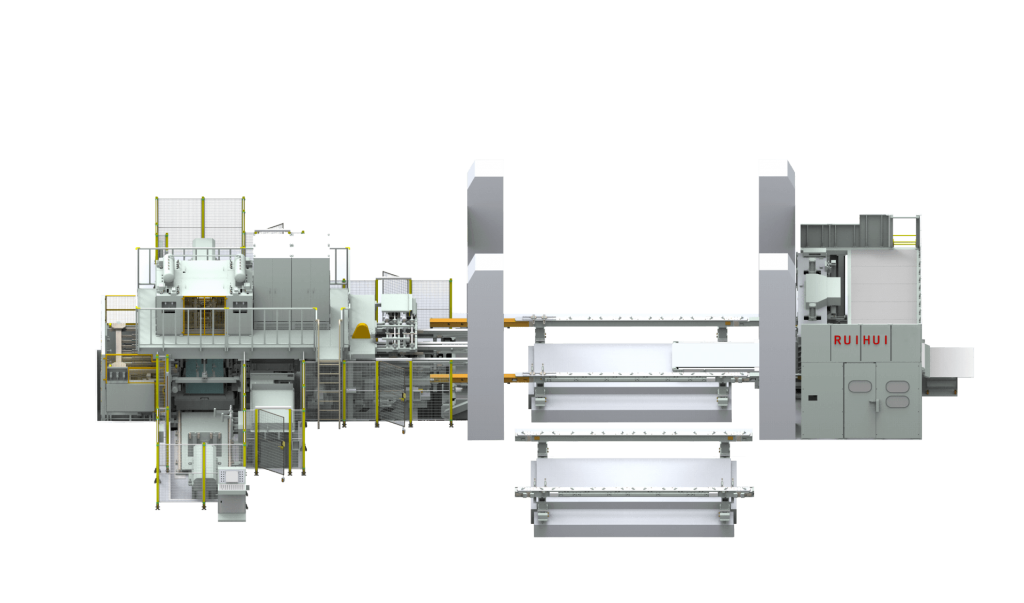
Industrial robotic arm
An industrial robotic arm is a “fixed or mobile machine. Its structure usually consists of a series of interconnected or relatively sliding parts for grasping or moving objects. It can complete active control, reprogrammable and multiple degrees of freedom. (Axis ) The working method is mainly to reach the target position through linear motion along the X, Y, and Z axes.
Industrial robot
According to the definition of ISO 8373, an industrial robot is a machine device that actively performs tasks. It is a machine that performs various functions through its own power and control ability. It can bear the command of human beings, and it can also run according to the pre-arranged programs. Modern industrial robots can also act according to the guidelines and guidelines established by artificial intelligence technology.
Stamping manipulator
It can replace the manual stamping, handling, loading and unloading of each stamping station, and the efficiency of the entire production line exceeds 5 seconds.
Automation equipment can reduce labor and labor costs, improve labor and equipment safety, and maintain product productivity, quality, and process stability for highly repetitive, high-risk, and fast-paced processing industries.
The flexible stamping automation line generally consists of a double-acting stretching press or a multi-link single-acting stretching press and 4 to 5 single-acting presses.
Manufacture of large body panels with high safety and high stamping quality.
The production line is equipped with an automatic loading and unloading system.
Stamping robot features:
1. The main drive is realized by high-performance servo motor;
2. It can realize fast positioning, lifting and moving;
3. Adopt custom-developed lateral translation structure and auxiliary lifting structure;
4. The whole machine uses a microprocessor to control and interlock the operation of the punching machine, and the operation and parameter setting are all carried out through the touch screen.

The difference between a robot and a robotic arm
Manipulator is a mechanical device employed in robotics. It is utilized across many industries, such as medical, military, aerospace, and more. Manipulators are divided into four-axis, five-axis, six-axis, multi-axis, 3D/2D robots, independent manipulators, hydraulic manipulators, etc. They share a common ability: receiving instructions and accurately locating points in either three-dimensional or two-dimensional space for calculation.
A robot and a robotic arm are different. A robot can accept instructions from humans and carry out tasks based on a pre-programmed program. It can also respond to guidelines dictated by Artificial Intelligence.
The difference between robots and manipulators in the scope of application:
Robotic arms are widely used in industry. The main technology it contains is drive and control. Robotic arms are commonly used in series.
Robots are divided into two types: series structure and parallel structure. Parallel robots (PM) are typically used in situations with high requirements for rigidity, precision, and speed. PM do not require a large space.
They are used in detail for sorting, handling, simulated motion, parallel machine tools, and metal cutting. Robot joints, spacecraft interfaces, etc.; serial robots, and parallel robots form a complementary relationship in the application.
The large working space of this series of robots prevents coupling effects between drive axes. However, each axis of the mechanism must be controlled independently, requiring encoders and sensors to improve the precision of the movement.