The top suction multi-station manipulator stamping production line is a highly efficient automated production line, which is widely used. The production line integrates multiple key processes such as stack dismantling, transmission, and stamping. Through automated operation processes, it realizes efficient and accurate conversion from raw materials to finished products, greatly improving production efficiency and product quality, while reducing labor costs and labor intensity.
So let’s start with the ingredients that you are most concerned about:
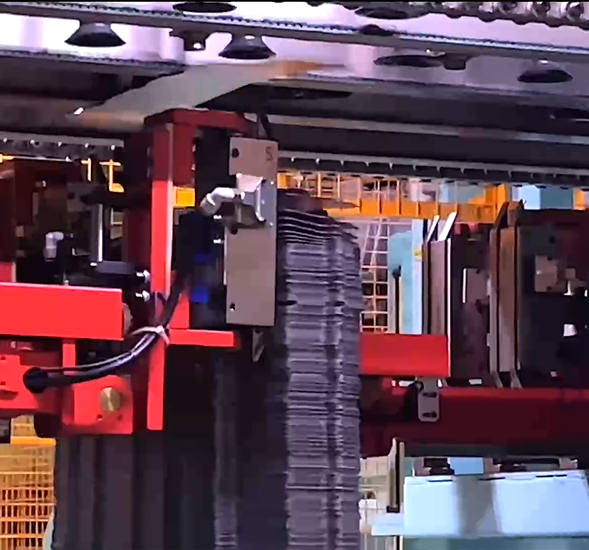
Top Suction Unstacker:It uses top suction technologies, such as vacuum suction or magnetic suction, to separate the stacked raw material sheets one by one and transport them to subsequent processes. For example, the vacuum suction cup forms a negative pressure environment when it closely adheres to the surface of the sheet, enabling it to firmly hold the sheet. Then, through the movement of the robotic arm, it precisely places the sheet on the conveyor belt. Compared with traditional side gripping methods, the top suction unstacker causes less damage to the surface of the sheet, which can better protect the quality of the raw materials. At the same time, it can flexibly adapt to sheets of different sizes, materials, and thicknesses, and has a high degree of versatility. In addition, the unstacker is generally designed with two or more stations. When one station is performing the unstacking operation, the other station can prepare for material loading, thus enabling an uninterrupted and efficient supply of materials.
Multi-station manipulator:A multi – station manipulator, driven by multiple servo motors, can move fast and precisely in 3D space. These motors, coordinated by a complex control system, accurately regulate the manipulator’s motion trajectory, speed, and force. When grasping a sheet, it adjusts position and angle based on the sheet’s state for accurate pick – up. During transport, it follows a preset path and precisely places the sheet at the target station.It’s highly flexible. It can swiftly adapt workflow and action sequences to different production processes and product needs. For example, when stamping various parts, it modifies the control program to change grasping, handling, and placing positions and methods. Moreover, it seamlessly interfaces with stamping equipment. During stamping, it feeds sheets into the mold accurately and promptly removes stamped parts, significantly boosting production speed.
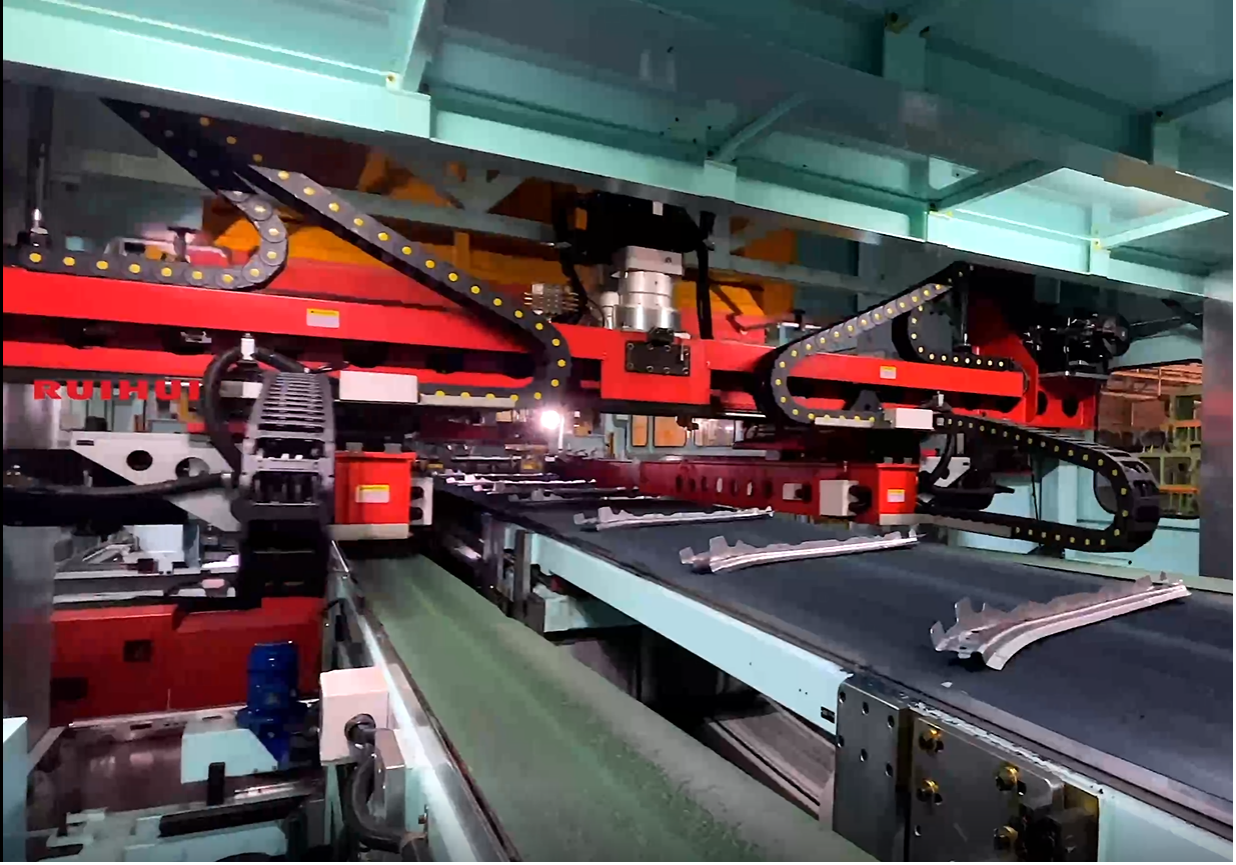
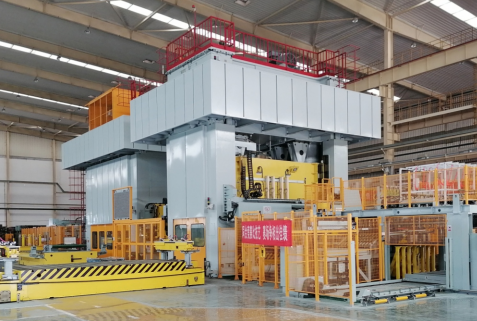
Prensa:In stamping lines, presses come in various types, mainly mechanical and hydraulic. Mechanical presses operate at high speed, making them efficient for mass – producing small – sized stamped parts. Hydraulic presses, on the other hand, generate high pressure. This makes them suitable for forming large and complex parts, with precise pressure control ensuring part quality stability.Dies on presses are crucial for product forming. Made with high – precision techniques, they ensure both the dimensional accuracy and surface quality of stamped parts. In auto body panel stamping, die precision is vital. It ensures the panels match the design, guaranteeing the car’s appearance and assembly quality.
After understanding the composition, understand the workflow:
Unstacking and feeding: The top – suction unstacker picks the top – most sheet from the stack via robotic – arm movement and places it on the conveyor belt, which has a positioning device for accurate sheet transfer.
Plate transfer: The conveyor with the sheet takes it to the cleaning & oiling stations. Special equipment cleans impurities, and lubricant is applied to reduce friction and protect the die.
Centering: After cleaning and oiling, the sheet reaches the centering station. Visual or mechanical means adjust its position precisely before it enters the stamping die.
Stamping forming: A multi – station manipulator sends the sheet to each stamping die for processes like stretching, punching, and bending, moving it fast and accurately between stations.
Blanking output: The robot removes finished parts from the last stamping station and puts them on the conveyor for inspection and packaging.
You can understand the workflow more intuitively through specific videos: