The compound 3-axis transfer stamping line is a multifunctional composite production line specifically designed to meet customer needs, integrating three-in-one progressive stamping and 3-axis multi-station stamping. It consists of NC straightener feeder, loading trolley, destacking manipulator, magnetic belt conveyor, 3-axis transfer, transfer bar, and exit conveyor. This production line integrates advanced automation control technology with an intelligent operating system, featuring high efficiency, high precision, and high stability. It is capable of both feeding coils into the press for stamping and delivering sheets into the press for stamping. Additionally, it can cut the coil into rectangular pieces via a shearing machine for subsequent stamping and forming. The combination of multiple automated equipment modes enhances the utilization rate of press and improves the ability to meet the demands of complex product variations.
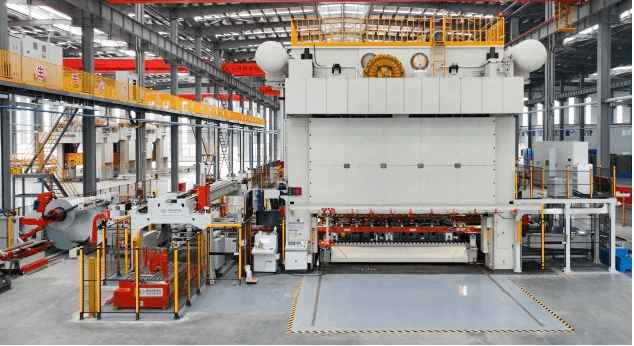
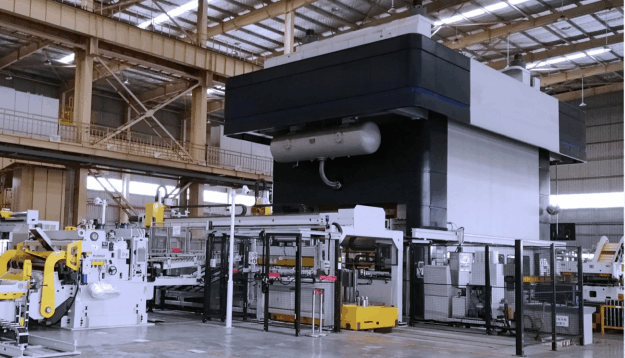
NC Straightener Feeder
The NC Straightener Feeder is composed of three parts: loading trolley, decoiler, and leveling-feeding machine. RUIHUI offers different solutions to optimize material feeding based on the material’s yield strength, weight, width, thickness, forward speed per stroke, and required flatness. Options include short lines, long lines, and movable mobile types. The NC (Numerical Control) technology allows for precise adjustments and real-time monitoring, enhancing the overall efficiency and accuracy of the feeding process.
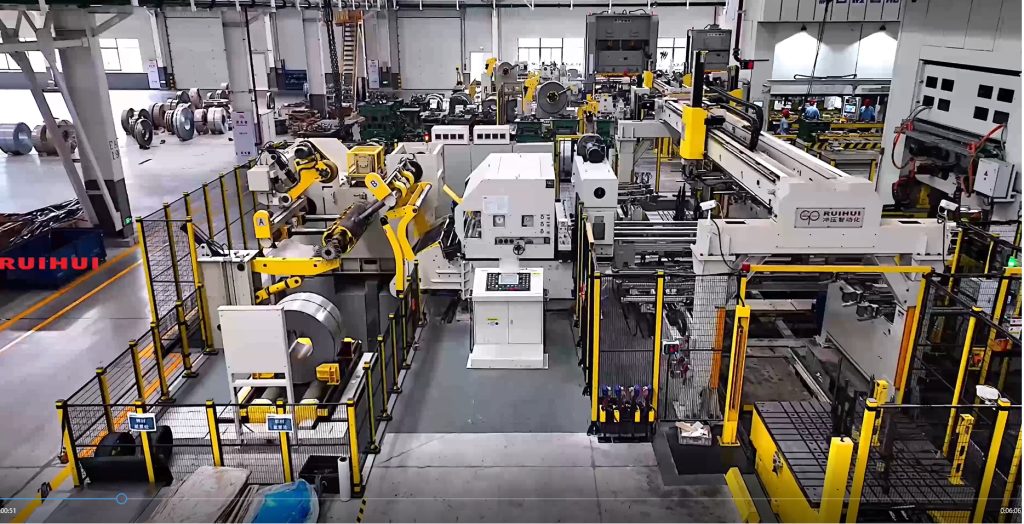
Loading Trolley
The loading trolley is designed to efficiently load the stacks onto the production line, reducing manual handling and increasing safety. It consists of a positioning and sheet-separating mechanism, trolley body, lifting mechanism, and control section. The stacking positioning rod and magnetic sheet separator are fixed on the upper surface of the trolley and move with it, using dedicated tooling for positioning and ascending/descending to the pickup position via a lifting rod mechanism.
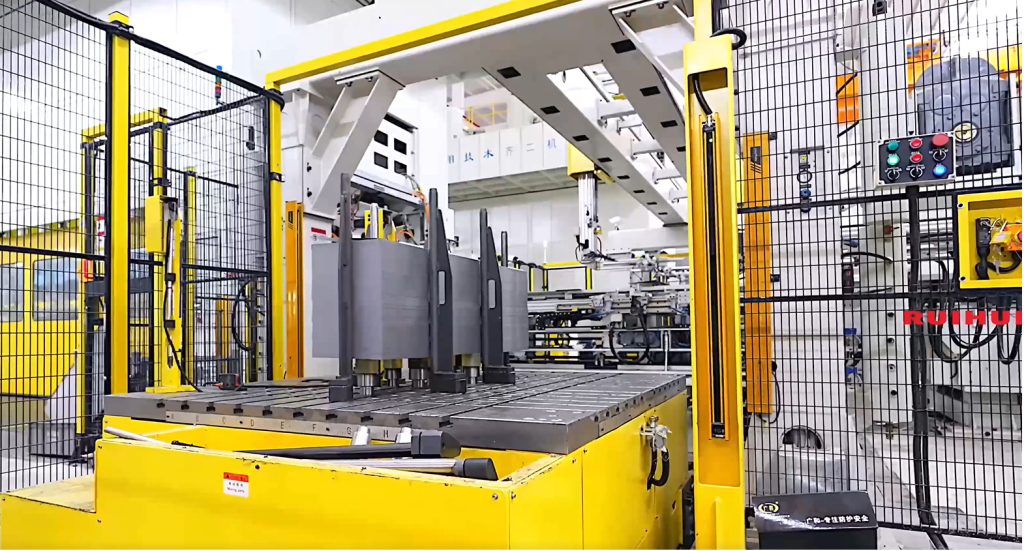
Destacking Manipulator
The manipulator is capable of automatically destacking and positioning individual sheet from a stack. The destacking system adopts two truss-type destacking manipulators that work alternately, which pick material sheets from different stacking trolleys onto the magnetic belt mechanism through control signals. During the rapid material-picking process, it operates steadily without shaking. Its lightweight structure, combined with a balancing cylinder, ensures stable and swift movement.
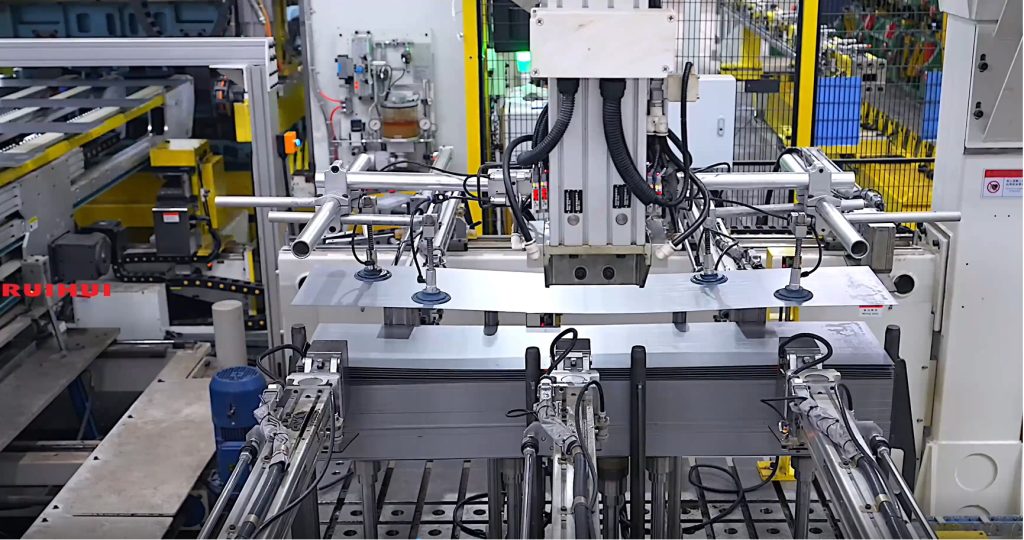
3-Axis Transfer
The manipulator consists of 3 axes. The 3 axes use gear and rack transmission, with Japanese linear guide accessories ensuring precision. It achieves linear motion with high rigidity and low friction, ensuring the positioning accuracy and repeated positioning accuracy of the manipulator under high-speed and heavy-load operating conditions.
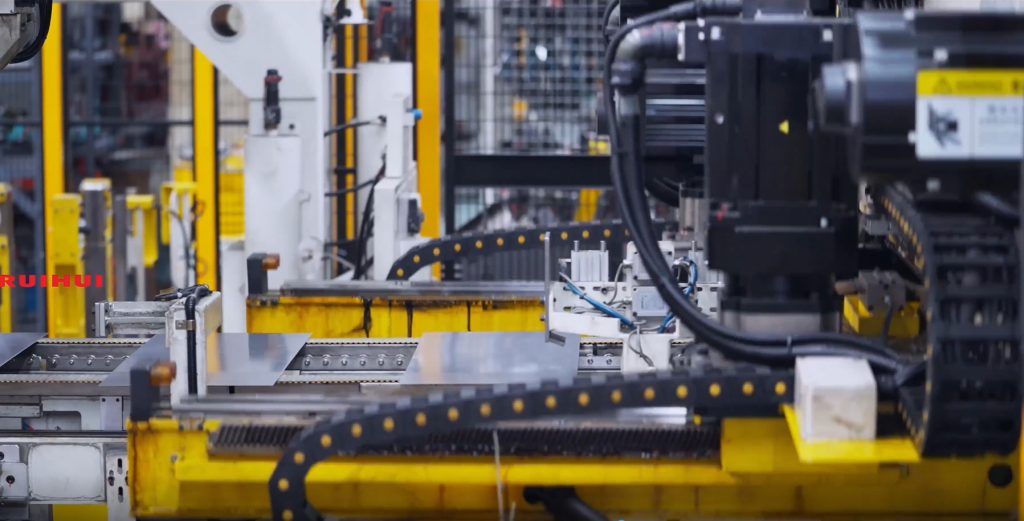
Transfer Bar
The conveying bar is composed of 3 sections, with the middle section of the cross bar being the mobile section, which automatically disassembles and assembles with the two sections on the main and auxiliary machines. The X-axis of the cross bar adopts an upper slide plate design to reduce the running load of the crossbar.
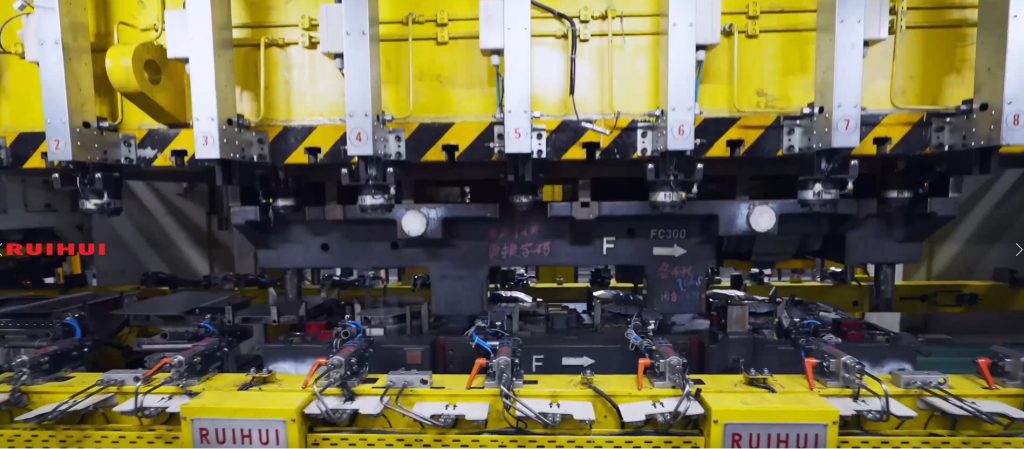
Exit Conveyor
The exit conveyor receives and transports finished products to the rear end for manual packing. The front section automatically telescopes to reduce the occurrence of empty die stations. The height adjustment is automatic to match feeding height of the die, which ensures accurate transfer of products, effectively avoiding issues such as jamming, collisions, or feeding errors caused by height deviations. This significantly enhances the overall line’s operational stability and the flexibility of die compatibility.
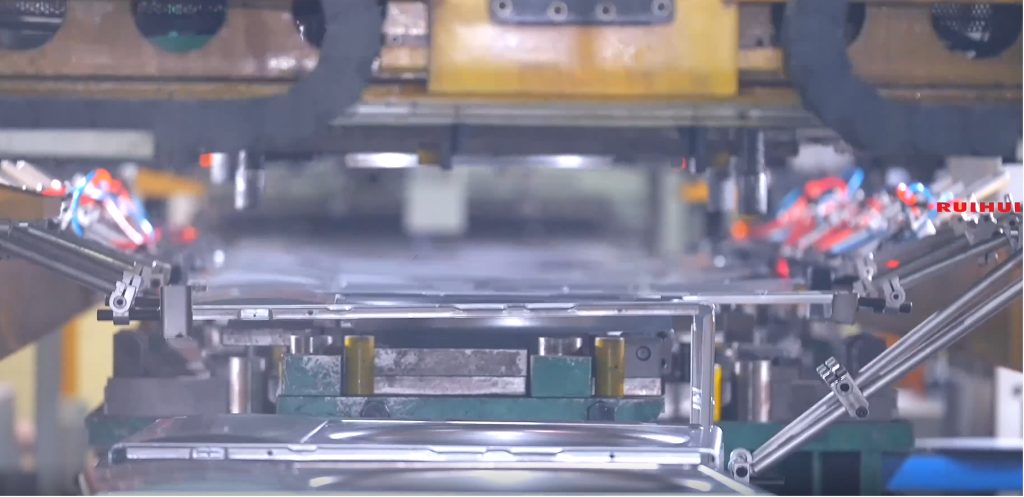
In recent years, with advancements in domestic capabilities in mold, press, and automation technologies, multi-station production lines have been widely adopted among Tier 1 and Tier 2 suppliers. The compound 3-axis transfer stamping line has emerged as a distinct competitive advantage in the industry, with its high operational efficiency, rapid cycle rates, broad product coverage, labor and cost reduction, highly automated production models, and improved material utilization.