As people’s demand for the quality of the living environment is getting higher and higher, the country is also imposing higher standards for environmental protection and energy efficiency in the automotive industry. Lightweight vehicle body has been an important issue to be implemented by each automobile manufacturer. The application of ultra-high-strength steel plate materials is one of the effective ways to realize vehicle lightweight and improve structural strength. However, traditional cold stamping processes present difficulties in forming high-strength steels and suffer from severe spring back, which greatly increases the complexity of tooling manufacturing and debugging. The emergence of hot-forming technology has perfectly resolved these two major challenges.
Hot forming production lines can be divided into multi layer heating furnace(MLF) and roller heat furnace production lines (RHF) according to different heating furnace designs. Ruihui provides automation solutions for both designs. Ruihui can provide integration and general package for the whole line, providing customers with complete turnkey solutions. Many domestic and international vehicle models have started to apply hot forming technology to their body structures, chassis, and components of new vehicles. The multi-layer box furnace hot forming automatic stamping line is suitable for both the hot forming process of ultra-high-strength bare steel plates and coated steel plates, as well as the warm forming process of high-strength aluminum alloy sheets.
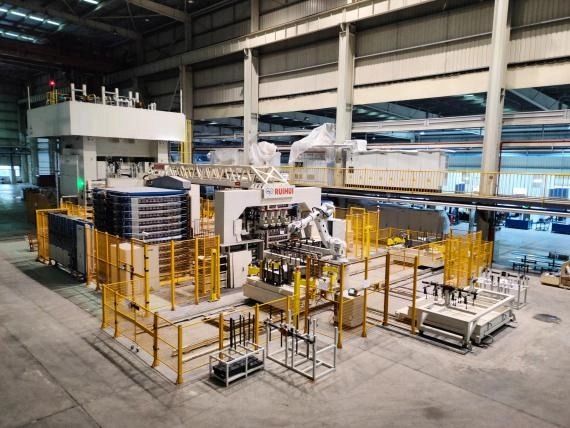
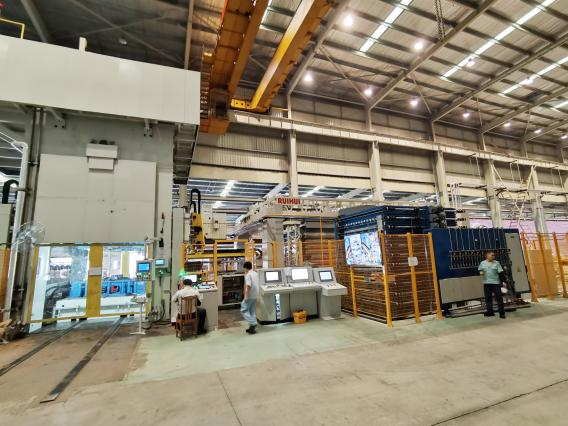
Stacking Trolley System
The trolley is manually loaded with material stacks outside the line, and it is equipped with positioning rods to ensure the accurate location of workpieces. The system adopts a dual-material stacking trolley design, with precise positioning of trays through recipe holes. Scales are provided on both sides of the trays for quick recall and positioning of process cards. The trolley is equipped with a toggle separator and a manual separator to gradually separate the material stack.
The dimension of the trolley is fully compliant with the production size requirements of the material sheets, maintaining stability during movement and enabling automatic travel when switching material stacks, thereby improving production efficiency.
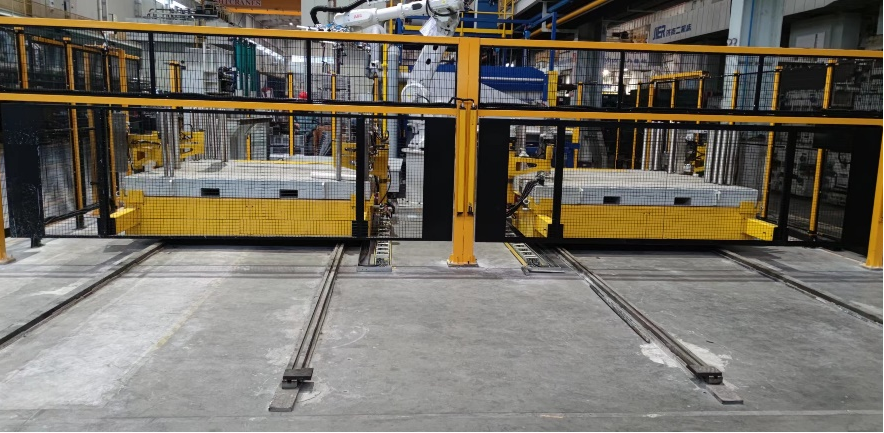
Robotic Destacking System
The robotic destacking system employs an advanced imported articulated 6-axis robot, which, with its excellent flexible movement capabilities, combined with a versatile end picker, can accurately separate stacks on the trolley and stably convey sheets to the coding machine for subsequent processing. The end picker is ingeniously designed to support quick replacement of the female end or automated replacement via a quick-change tool plate, greatly enhancing the adaptability and work efficiency of the system. The system is equipped with an independent teaching pendant for operation and control, which can automatically identify and adjust the stack height to ensure precise material destacking every time. Additionally, the teaching pendant supports individual control of the material discharge action, making the operation more flexible and controllable.
Furthermore, the system integrates multiple vacuum generators for precise control of the material gripping process. These vacuum generators work in synergy to ensure the stability and reliability of the material during gripping, further enhancing the overall performance of the system.
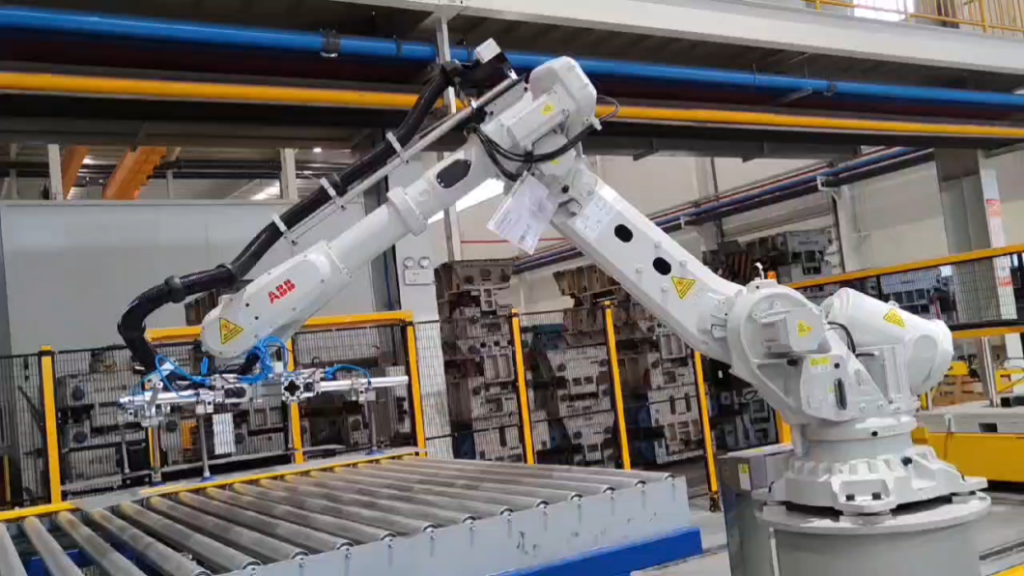
Special Shuttle Car For Box Furnace
The feeding and unloading manipulator consists of 2 sets of mechanisms, each of which has 4 moving functions: lifting, telescopic, rotating, and lateral. The current design of this model can adapt to the production of 11-layer heating furnaces. The feeding manipulator takes the cold material from the centering table and moves it through 4 mixed actions to put the cold material into the empty furnace layer. The hot material manipulator quickly takes out the hot material through the feedback signal from the heating furnace and quickly transfers it to the gripper of the press feeding manipulator through 4 mixed movements, and then quickly puts the hot material into the mold through the manipulator.
The receiving fork is made of special material, with small vibration during fast operation and small deformation due to heat. A large turntable structure is used at the up and down rotation positions to ensure the stability of the entire structure when rotating on the R axis. It effectively overcomes the defect of poor dynamic stability of the commonly used single-point cantilever beam structure and realizes the rapid movement of feeding and discharging materials.
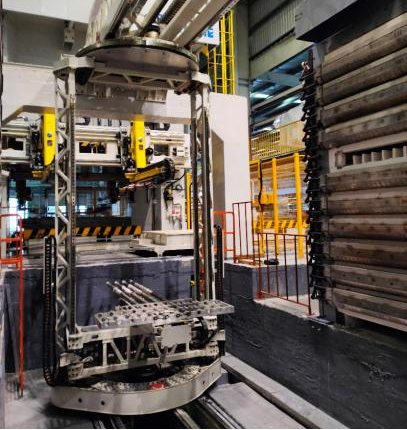
Box Type Furnace Charging Centering Platform
The destacking manipulator places the sheet material onto the servo-controlled centering platform, which then lifts the sheet up. The sheet is centered and positioned by a tapping mechanism that taps it into place. After the sheets are depalletized and coded, the sheets are positioned by beating them with multiple beaters on the centering table, taking into account factors such as the misalignment of the material stack on the trolley, so that the sheets can be quickly introduced into the positioning ring of the receiving fork, and the heating furnace can protect the materials from collision. There are 16 sets of beaters on the positioning table, which are driven by independent servo motors and can adapt to the sheet beating capacity of 1 mold and 4 cavities. The positioning is accurate, the loading speed is improved, and the loading time is reduced. The width of the positioning rod can be adjusted to accommodate the beating and positioning of large and small and irregular-shaped materials.
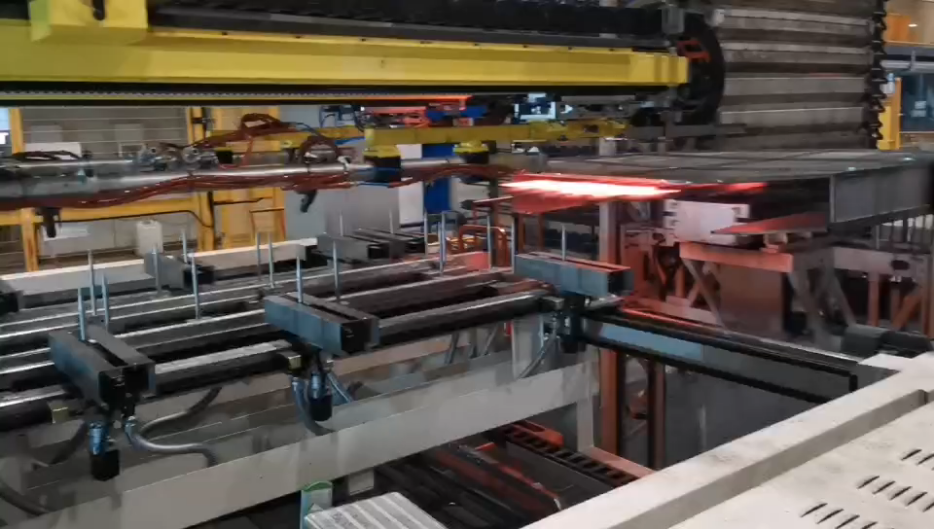
Press Loading and Unloading Robot
The 3-axis manipulator adopts servo drive and has two working modes: TRANSFER and FEEDER. Through real-time detection of the position of the slider during the stamping process of the press, the position of the slider is compared with that of the loading and unloading manipulator during the pressing process. The control system has a synchronous motion control software function to ensure that the press and the manipulator are always kept within a safe distance.
The X-axis adopts a double-speed structure, and a manual quick-change structure is installed on the double-speed moving plate. Each set of molds corresponds to a set of grippers, and manual quick-change is used to meet the gripping of different mold workpieces. The air circuit and electrical signals are connected by manual quick plugs. The loading and unloading manipulator can be moved to one side as a whole when changing the end picker, and the manipulator box extends beyond the press column to facilitate manual replacement of the gripper.
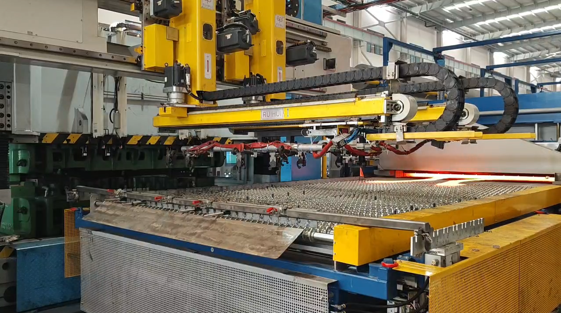
Line Tail Discharge Conveyor Belt
The tail conveyor can be of chain plate type or mesh type, and it has high temperature-resistant conveying capability. The hot stamped parts are transported to the parts conveyor by the press unloading manipulator, and the conveyor transports the parts to the manual unloading position at the tail end. There is a fan on the top to cool the workpiece. The operating box is installed at the end of the line body, including an emergency stop button, and switches for selecting stepping and emptying functions. The conveyor is driven by a reduction motor with frequency conversion control for smooth and precise operation.
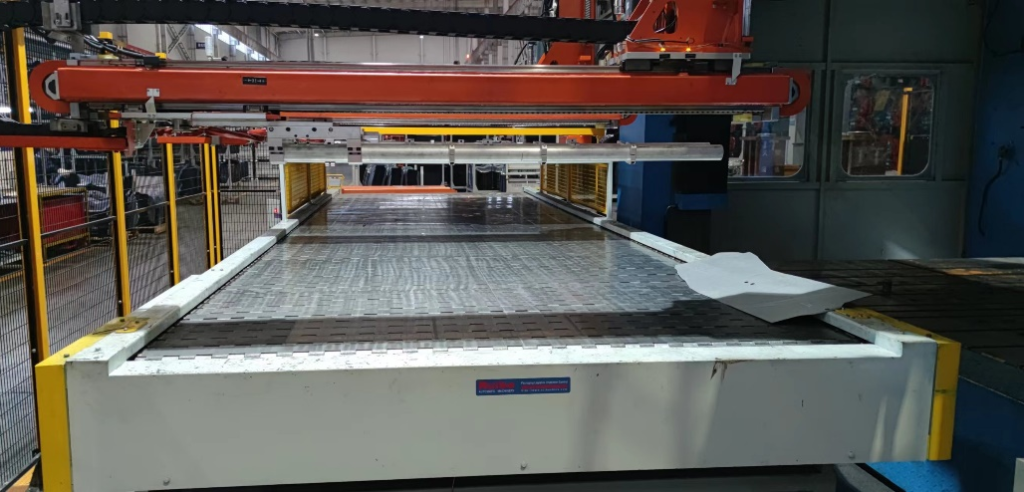