The equipment composition of the stamping thermoforming line is mainly composed of automation, presses and heating furnaces. In fact, the presses and heating furnaces use automation equipment to carry out in-line production and automatic control.
The Composition Sequence of Main Equipment:
Unstacking System (Automation Category)
Stacking platform/trolley, according to the production process and production cycle requirements, the stacking platform used can be divided into loading platform or trolley, in order to save time for replacing stacking materials, some use 2 stack loading tables or 2 stack loading trolleys.
A magnetic separator is set on the stacking platform to separate the boards, and a positioning rod is set on the loading platform to place and position the stacking material according to its benchmark.
The depalletizing robot, with a vacuum end picker, separates and absorbs the stacked materials, and detects whether the boards are double materials. According to the production process, the steel plate is engraved and coded. Put the coded steel plate into the entrance platform of the heating furnace.
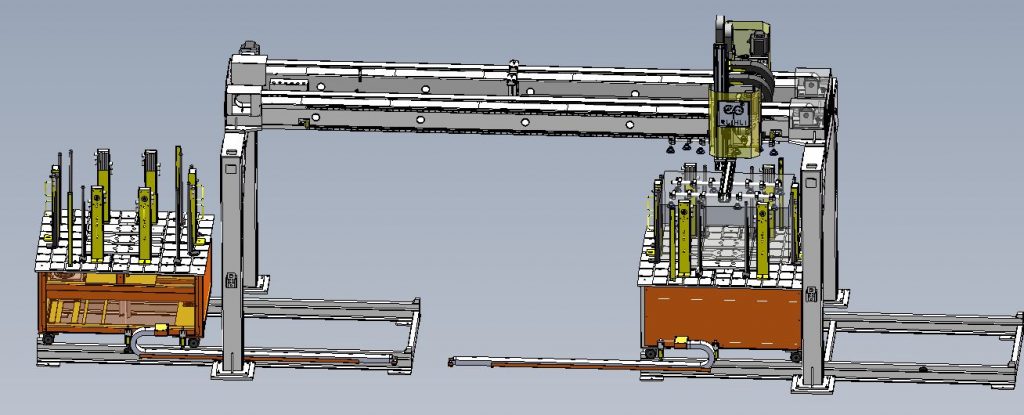
Heating Furnace (Heating Furnace Manufacturer)
It is divided into the bottom continuous road and box type heating furnace, with electric heating and gas heating, and electric mixed heating. Common manufacturers include Sanjian, Swartz, Abner, Benteler, etc. Furnaces usually contain centering stations at the end.
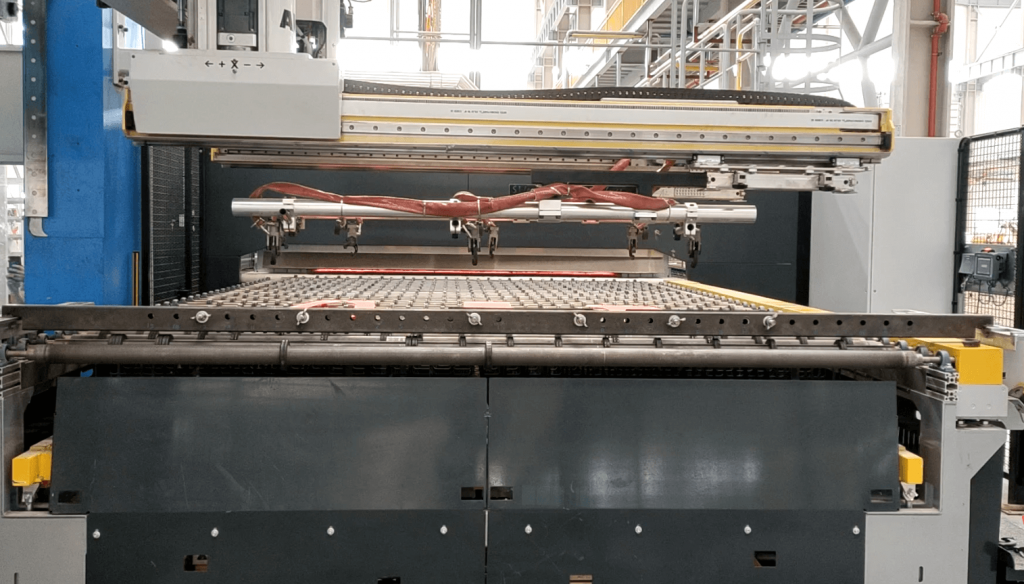
Press (Molding Equipment)
Hydraulic press or servo hydraulic press is usually used. Commonly used press manufacturers include Kawasaki Oil Works, Amino, Taiwan Union, and Taiwan Association Ytterbium.
Feeding Manipulator (Automation Category)
It is required to send the heated steel plate to the press within 1.5 seconds. The feeding manipulator needs a double-speed mechanism, and it needs to be moved into the forming press efficiently, quickly and stably. A clamping device is provided on the end effector, and the temperature is detected.
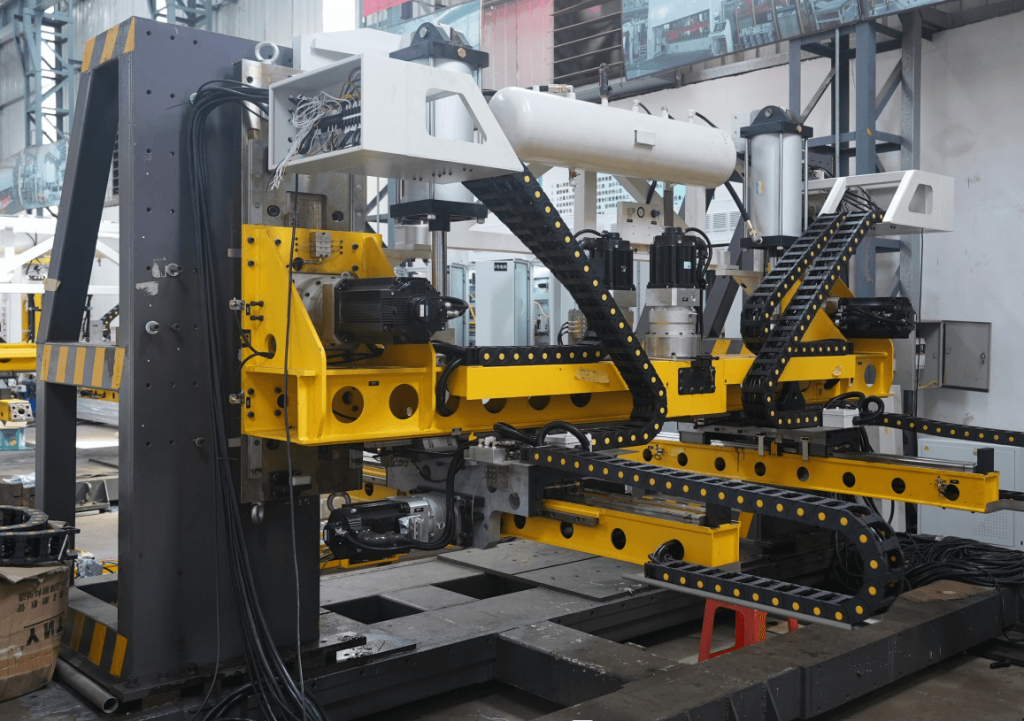
Unloading Manipulator (Automation Category)
It is required to take out the formed steel plate within 1.5 seconds and place it on the discharge iron mesh belt conveyor.
The integration of the entire system also falls under the category of automation. In order to improve production efficiency and realize the automation manufacturer of synchronous curve control of heating furnace and press, our company currently has relevant cooperation with Japan’s Oyabe Seiki Co., Ltd.